Bicomponent fibers or ‘‘heterofil’’ fibers are filaments made up of different polymers. There
are many geometrical arrangements. The three main heterofil geometries are side-by-side,
core–sheath (both concentric and eccentric), and the multiple core or ‘‘islands in a sea’’
configuration. The so-called ‘‘splittable pie’’ configurations are used in the production of
microfibers (see Figure 1.12).
The two polymer components do not have to differ in ‘‘chemical’’ nature. They can
differ only in physical parameters such as molecular weight. Usually, it is desirable that the
two components have good mutual adhesion, but not always. Polyolefines do not bond well
with polyesters or polyamides and this fact is exploited in the formation of microfibers (see
later).
SIDE–SIDE BICOMPONENT FIBERSSide–side bicomponent fibers can be used to produce self-bulking yarns. Two PET polymers
of different molecular weights, spun as a side–side heterofil, produce a self-bulking fiber
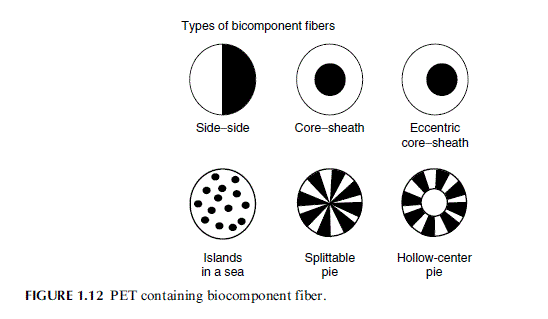
after drawing and relaxing because the spun birefringences differ. The relaxed yarn curls up
like a bimetallic strip and results in a spiral crimp. A self-bulking fiber can also be made by
cospinning PET with a PET copolyester containing a branching agent in a side–side configuration
[66].
CORE–SHEATH BICOMPONENT FIBERS
The core–sheath (c–s) configuration is adaptable because many different polymers may be
applied as a sheath over a solid polyester core, thus giving a variety of modified surface
properties while maintaining all the major fiber and textile properties of PET. An early patent
by Shima and coworkers uses an eccentric core–sheath configuration to achieve spiral crimp
in a yarn [67]. A recent patent by Chang and coworkers discloses the use of side–side or
eccentric c–s bicomponent fibers to achieve a self-crimping yarn made from polytrimethylene
terephthalate, where one component is a melt-blend of PTT with a small amount of polystyrene
[68].
We have already mentioned the antisoil–antistatic fiber made by using a PET–PEG block
copolymer coating on a polyester core. A widely used c–s heterofil has a normal PET core
with a lower softening-point sheath polymer (typically a PET–isophthalate copolyester).
When such fibers are laid randomly in a nonwoven structure and heated to a temperature
above the softening point of the sheath polymer, but below the fusion point of the core
polymer, the fibers adhere wherever they cross and touch. This may be done either by heated
calendar rolls or simply in a forced draught hot air oven. The result is a stable nonwoven
fabric [69,70]. A new development is a biodegradable, nonwoven material for disposable
fabrics, made by thermally bonding a polylactide core bicomponent fiber with a low melting
sheath polymer such as polyethylene [71].
MULTIPLE CORE BICOMPONENT FIBERS
The multiple core or ‘‘islands in a sea’’ type of heterofil is mainly of interest in connection
with microfibers and this is discussed in the following text.
HOLLOW FIBERS
Hollow fibers are a type of core–sheath heterofil in which the core is composed of air.
They are usually made in the form of crimped staple fiber and spun from a modified staple
spinning pack [72]. With advances in melt-spinner design, more complex geometries [73]
are available. One patent describes a multiple-core circular polyester staple fiber with seven
cores [73]. Hollow fibers in the form of filament yarn have specialized uses in medical
devices, but the largest volume market for hollow fiber is staple fiberfill for pillows, duvets,
quilts, and thermal outerwear. The desired quality here is ‘‘loft’’ and it is better if the fiber
is light and bulky. The most desired quality is thermal insulation. Hollow polyester
fibers are well suited to this end use: the air entrapped in the hollow cores adds significantly
to their insulating properties; more hollow air cores increase this effect. The fibers
are frequently crimped by a stuffer-box process or made as bicomponent hollow fibers,
which develop spiral crimp on drawing. Such filler fibers are frequently treated with a
permanent polysiloxane finish that makes them slippery, so that they slide easily over each
other and resist clumping up, which reduces their insulating effect. In this form, they
compete with goose down as a thermally insulating filling material. For end-uses like
fabric interlinings, it is desirable to stabilize a filled hollow fiber structure by incorporating
an additional thermally bondable bicomponent fiber [75].