The melt spinning of PET has been extensively treated in the patent literature, but less in the
open literature [27], although the recent chapters by Bessey and Jaffe [28] and Reese are
good introductions to the process. We will concentrate here on how changes in the key
process variables of spinline stress and temperature profile affect assembly at the molecular
level (morphology), and, in turn, how the morphology affects the resulting performance of the
yarn. The relationships described here are equally valid for all semicrystalline polymers; LCPs
will be treated separately. The average value of key properties and the standard deviation
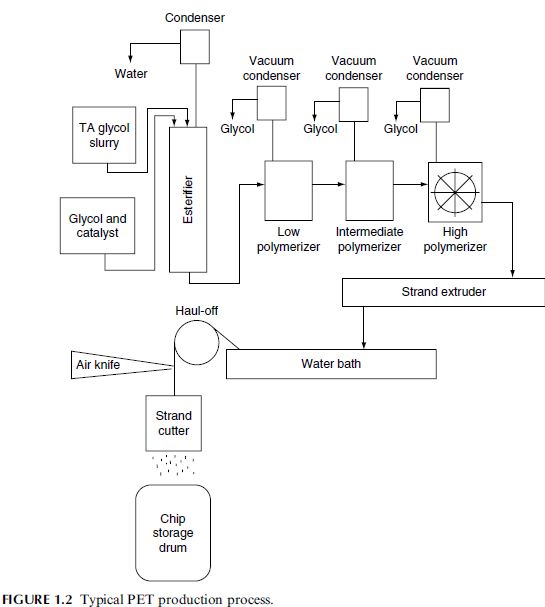
associated with the mean value must be controlled for fiber products to have commercial
value. In general, variation in properties, hence variation in morphology, must be controlled
to about 10% for the yarn to be commercially acceptable. Variation means differences
between filaments in a yarn or along a given filament. The frequency of variation is also
critical; high frequency changes that may be averaged over a critical use length are, in general,
more acceptable than a smaller variation along or between filaments that occurs at a lower
frequency.
Polymer is introduced into the manifold of the spinning machine either as a dried chip or
as produced by the CPU. The manifold may feed as few as one or as many as 200 separate
spinnerets and is designed to keep the directed polymer streams as uniform as possible in
shear and thermal history. The PET spinning temperature is typically between 280 and 3008C;
local shear heating may increase this temperature by as much as 10–158C. The molten
polymer stream is then fed through metering pumps to the spinning pack (assembly that
starts with a series of filters and ends at the spinneret—see Figure 1.3). The spinneret consists
of five (hosiery yarn) to several thousand holes, typically ranging from 180 to 400 mm in diameter. Pack and spinneret designs are the subject of specialized expertise and the reader is
referred to the open and patent literature for the depth of engineering detail available on these
subjects [29]. The purpose of pack and spinneret is to insure that filtered (clean) polymer is fed
to each hole of the spinneret as uniformly as possible. Passage through the spinneret subjects
the polymer to a complex rheological environment (see, for example, the work of Denn [30]),
resulting in local increases of molecular orientation and a distribution of orientation between
the spinneret wall and center line. On exiting the spinneret, the combined effects of surface
tension and relaxation of molecular orientation result in die swell (increase of the filament
diameter to greater than the spinneret hole diameter).
From a molecular point of view, the starting polymer melt is best visualized as an
entangled network, characterized by the polymer molecular weight, molecular weight distribution,
the entanglement density, and the average chain length between entanglements. This
is shown diagrammatically in Figure 1.4.
The processes that occur in the spinline, between the exit of the polymer from the
spinneret and the point of stress isolation on the first godet or roller at the base of the spin
line, involve the changing of this fluid network to the solid-state molecular chain topology of
the filament. Within a distance of 3–5 m, and under the influence of an applied force (take-up
tension) and quench media, at speeds in excess of 100 miles per hour—less than 0.01 sec
residence time—the fiber is transformed from a fluid network to a highly interconnected
semicrystalline morphology, characterized by the amount, size, shape, and net orientation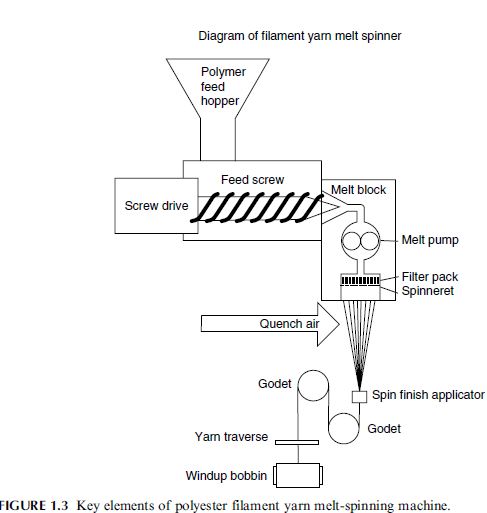
(with respect to the fiber or long axis) of crystalline units, and the orientation of spatial
distribution of noncrystalline areas. All of these units are interconnected by molecules that
traverse more than one local region (tie molecules) of the load-bearing elements of the fiber
structure.
It has been noted [31] that the crystallization rate of polymers increases by up to six orders
of magnitude when the crystallization event occurs when the polymer is under an applied
stress rather than in a quiescent state. This large increase in crystallization rate is accompanied
by a change in crystal habit, the shape of the crystalline phase produced transformed,
over a narrow stress regime, from a spherulitic (spherically symmetrical) to a columnar habit
(see Figure 1.5).
This transition is surprisingly sharp—occurs at a stress of about 0.1 g=d. Increasing the
spinline stress increases the number of rows and decreases the diameter of the fibrillar
structure. As the fibrils are stable only in the presence of the spinning stress, they may or
may not be visible in the final fiber morphology. A useful way of conceptualizing the process
is to divide the spinline into three regions, namely:
. Region 1. Increase local and global molecular orientation
. Region 2. Fibril formation at points of maximum orientation (transient mesogen,
mechanical steady state)
. Region 3. Fibril decoration (folded chain crystal growth)
A cartoon of this model of morphology and molecular chain topology development in melt
spinning of PET is shown in Figure 1.6.
In Region 1, the spinline stress leads to filament drawdown, causing a net increase of
molecular orientation of the molten and amorphous polymers. A consequence of this stress is
the disentangling of some of the starting network chains and the increase in the local
molecular chain orientation in the proximity of remaining entanglements. As these bundles
of locally oriented chains grow in aspect ratio, they satisfy the conditions for nematic phase
formation [32–34], leading to a biphasic array comprised of fibrillar mesogenic structures
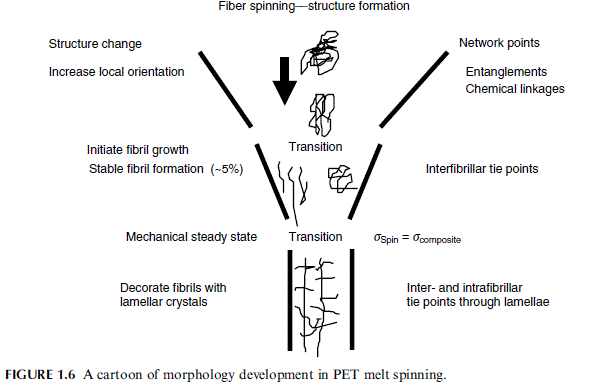
sitting in a lesser oriented amorphous matrix. When the spinline stress is completely supported
by these fibrillar structures, the matrix chains are able to relax and the conditions for
fibril formation are no longer extant. As one enters the lower temperature ranges, the fibril
acts as an effective high nucleation density for lamellar crystal overgrowth of the fibrils,
leading to increases of up to six orders of magnitude in the effective crystallization rate.
Fibrils may or may not be evident in the final structure, but the high orientation of the wholly
semicrystalline structure is always evident. The transient fibrillar structures act as the template
for all further structure formation. It is also evident that molecular chains can participate
in more than one element of the structure; these tie molecules provide the stress transfer
elements as subsequent fiber deformation [35]. Conceptually, three types of tie molecules
are possible in the model: interfibrillar, interlamellar (between lamellae on a given fibril or
between lamellae on different fibrils), and between fibril and lamella. It is the tie molecule
distribution, combined with the remaining entanglement distribution, that defines the residual
draw ratio of the fiber structure [36].
The detailed proof of this conceptual model is difficult experimentally, although it is generally
supported by the existing experimental data and melt spinning process model. The overall
veracity of the model is less important than the utility of the model in predicting process–
structure–property relationships. Important implications of the model are as follows:
. The order of molecular chain orientation and crystallization steps in fiber spinning is
critical.
8 The formation of a transient fibrillar mesophase is the template for all further
morphology development and defines the nucleation density for subsequent crystallization.
. As chain orientation prior to crystallization is increased, the load-bearing aspects of the
crystalline network produced also increases, while the noncrystalline load-bearing elements
of the structure decrease.
8 Leads to the decoupling of molecular orientation responsible for increased modulus
and strength, from oriented chains responsible for entropic shrinkage, allowing for
high modulus low shrinkage fiber products.
. The network defined in spinning remains the template for structure formation in all
subsequent processing steps.
The melt spinning of all semicrystalline polymers can be fit into the general framework
described above. Details of specific PET melt spinning processes are well documented in
the chapter by Reese, Bessey, and Jaffe, or in the papers of Ward. The structural state of the
spun yarn, while complex, is often described by a single parameter: the spun yarn birefringence,
an average measure of orientation. Jaffe has shown that the spun yarn shrinkage is an
excellent predictor of the remaining yarn draw ratio as shown in Figure 1.7 [33], where
DRmax is defined as the highest stable draw ratio available to a given spun yarn.